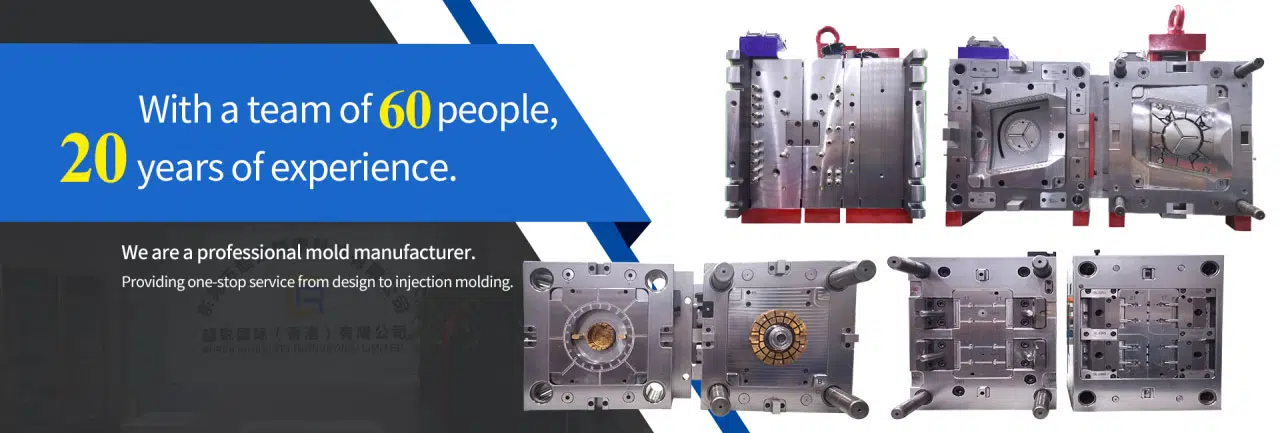
,文章长度约1000词。
html
Moldflow Simulation in Injection Molding Process Optimization
Injection molding is one of the most widely used manufacturing processes for producing plastic parts. However, achieving optimal results requires careful consideration of various factors such as material selection, mold design, and processing parameters. This is where Moldflow simulation comes into play, offering a powerful tool for optimizing the injection molding process.
Understanding Moldflow Simulation
Moldflow simulation is a computer-aided engineering (CAE) tool that allows manufacturers to analyze and predict the behavior of plastic materials during the injection molding process. By creating a virtual model of the mold and simulating the injection process, engineers can identify potential issues before physical production begins.
The simulation software uses advanced algorithms to model:
- Material flow patterns
- Cooling rates and temperature distribution
- Warpage and shrinkage
- Stress distribution
- Gate locations and filling patterns
Key Benefits of Moldflow Simulation
1. Reduced Development Time and Costs
Traditional trial-and-error methods in injection molding can be time-consuming and expensive. Moldflow simulation significantly reduces the number of physical prototypes needed, allowing for faster product development cycles and lower tooling costs.
2. Improved Part Quality
By predicting potential defects such as sink marks, weld lines, and air traps, engineers can make necessary adjustments to the mold design or processing parameters before manufacturing begins. This leads to higher quality finished products with fewer defects.
3. Optimized Material Usage
The simulation helps determine the optimal amount of material needed for each part, reducing waste and improving cost-efficiency. It also allows for evaluation of different material options to find the best performance-to-cost ratio.
4. Enhanced Mold Design
Moldflow analysis provides valuable insights into gate locations, runner systems, and cooling channel design. This information helps create molds that produce parts with minimal warpage and consistent dimensional accuracy.
Applications in Process Optimization
Moldflow simulation plays a crucial role in various aspects of injection molding process optimization:
Filling Analysis
The software predicts how the molten plastic will flow through the mold cavity, helping engineers identify potential flow imbalances or hesitation marks. This information is used to optimize gate locations and sizes, as well as injection speed profiles.
Cooling System Design
Proper cooling is essential for cycle time reduction and part quality. Moldflow simulation analyzes heat transfer and cooling efficiency, enabling designers to create optimal cooling channel layouts that ensure uniform cooling throughout the part.
Warpage Prediction
By simulating the cooling and solidification process, the software can predict potential warpage issues caused by uneven shrinkage. This allows for proactive design changes to minimize dimensional variations in the final product.
Fiber Orientation Analysis
For fiber-reinforced materials, Moldflow can predict fiber orientation patterns that affect mechanical properties. This information helps engineers design parts that meet specific strength requirements.
Implementing Moldflow Simulation
To effectively implement Moldflow simulation in the injection molding process, manufacturers should follow these steps:
Keyword: Moldflow Simulation
- Create an Accurate 3D Model: Start with a precise CAD model of the part and mold assembly.
- Define Material Properties: Select the appropriate plastic material from the extensive database or input custom material properties.