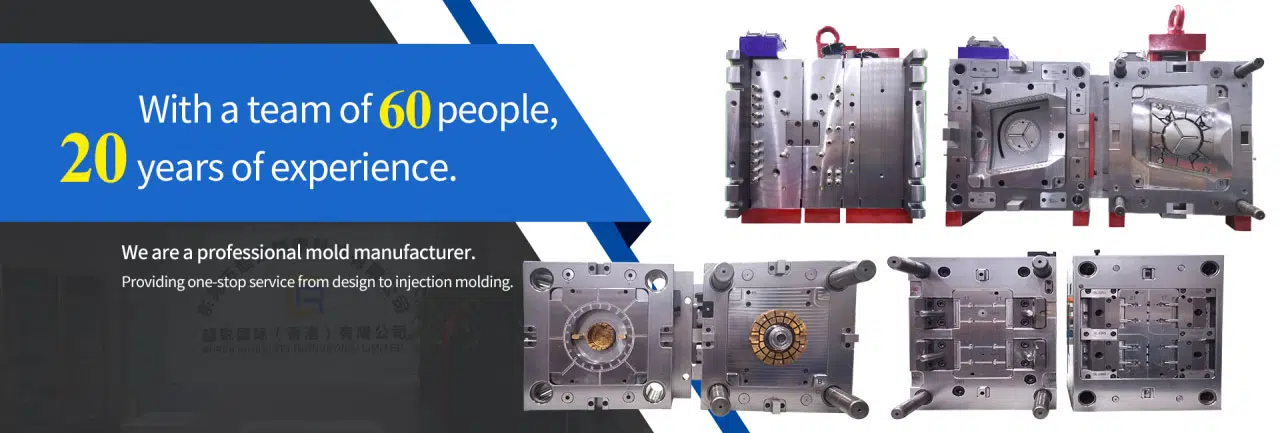
# Design for Manufacturing Analysis in Product Development
## The Importance of DFM Analysis
Design for Manufacturing (DFM) analysis has become a critical component in modern product development processes. This systematic approach evaluates product designs to ensure they can be efficiently and cost-effectively manufactured while maintaining quality standards. By incorporating DFM principles early in the design phase, companies can significantly reduce production costs, minimize defects, and accelerate time-to-market.
## Key Principles of DFM Analysis
1. Simplification of Design
One of the fundamental principles of DFM is simplifying product designs without compromising functionality. This involves reducing the number of components, minimizing complex geometries, and standardizing parts wherever possible. Simplified designs typically require fewer manufacturing steps and less material, leading to lower production costs.
2. Material Selection
Choosing appropriate materials is crucial for manufacturability. DFM analysis evaluates material properties, availability, and processing requirements to ensure compatibility with manufacturing capabilities. The right material selection can improve product performance while reducing machining time and tool wear.
3. Tolerance Optimization
DFM emphasizes setting realistic tolerances that balance product requirements with manufacturing capabilities. Overly tight tolerances can dramatically increase production costs without providing meaningful benefits to product performance.
## Benefits of Implementing DFM Analysis
Cost Reduction
Keyword: DFM Analysis
By identifying potential manufacturing issues early, DFM helps avoid costly redesigns and production delays. It typically leads to 20-50% reductions in production costs through optimized designs and processes.
Improved Quality
Products designed with manufacturing in mind tend to have fewer defects and higher reliability. DFM analysis helps eliminate design features that are prone to quality issues during production.
Faster Time-to-Market
With fewer design iterations and smoother production ramp-up, companies can bring products to market more quickly. DFM reduces the back-and-forth between design and manufacturing teams.
## DFM Analysis Techniques
1. Design Review Meetings
Cross-functional teams including designers, engineers, and manufacturing specialists collaborate to evaluate designs from multiple perspectives.
2. Computer-Aided DFM Tools
Specialized software analyzes digital models to identify potential manufacturing challenges, calculate cost estimates, and suggest design improvements.
3. Prototype Testing
Physical prototypes help validate manufacturability and identify issues that might not be apparent in digital models alone.
## Challenges in DFM Implementation
While DFM offers numerous benefits, implementation can present challenges. These include resistance to change from design teams, the need for cross-functional collaboration, and balancing DFM principles with other design requirements like aesthetics and functionality. Successful DFM implementation requires strong leadership commitment and ongoing training.
## Future Trends in DFM Analysis
Emerging technologies like artificial intelligence and machine learning are transforming DFM analysis. These tools can predict manufacturing issues with greater accuracy and suggest optimal design alternatives. Additionally, the growing adoption of additive manufacturing is creating new DFM considerations as designers explore geometries that were previously impossible to produce.
As product lifecycles shorten and competition intensifies, DFM analysis will continue to play a vital role in helping companies develop better products faster and more cost-effectively.