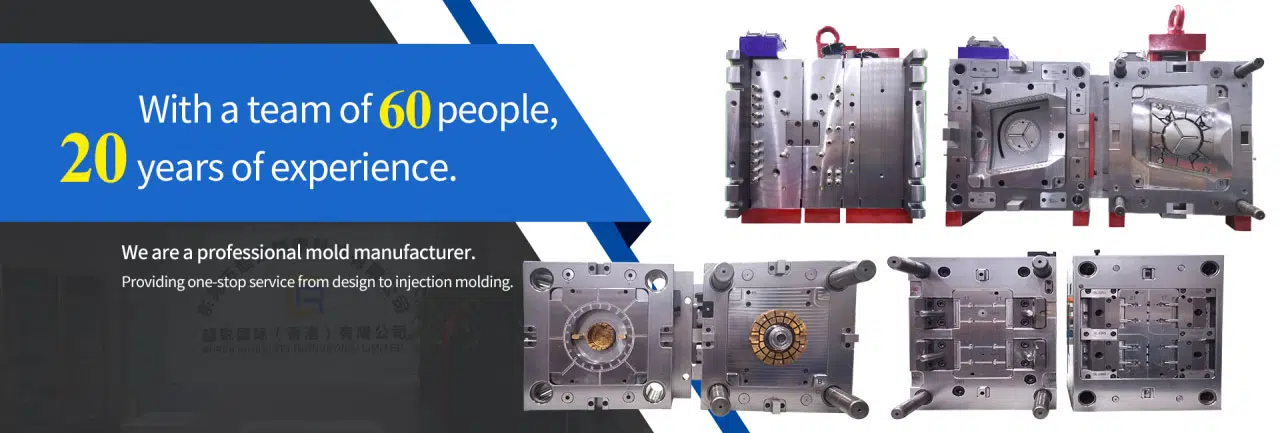
# Digital Manufacturing: Revolutionizing Production Processes
## The Rise of Digital Manufacturing
Digital manufacturing represents a paradigm shift in how products are designed, produced, and delivered. This transformative approach integrates computer systems throughout the entire manufacturing process, creating a seamless digital thread from concept to customer.
Unlike traditional manufacturing methods, digital manufacturing leverages cutting-edge technologies to optimize every aspect of production. It’s not just about automating existing processes but fundamentally rethinking how manufacturing should operate in the digital age.
## Key Technologies Driving the Revolution
Several groundbreaking technologies form the foundation of digital manufacturing:
– Industrial Internet of Things (IIoT): Networks of connected devices and sensors that collect and share data in real-time
Keyword: Digital Manufacturing
– Additive Manufacturing: 3D printing technologies that enable complex geometries and on-demand production
– Artificial Intelligence: Machine learning algorithms that optimize processes and predict maintenance needs
– Digital Twins: Virtual replicas of physical systems that allow for simulation and testing
– Cloud Computing: Scalable infrastructure for data storage and processing
## Benefits of Digital Manufacturing
The adoption of digital manufacturing brings numerous advantages to businesses:
### Increased Efficiency
By eliminating manual processes and reducing human error, digital manufacturing significantly improves production efficiency. Automated systems can operate continuously with minimal downtime, while predictive maintenance prevents unexpected equipment failures.
### Enhanced Customization
Digital technologies enable mass customization at scale. Manufacturers can quickly adapt production lines to create personalized products without sacrificing efficiency or increasing costs substantially.
### Improved Quality Control
Real-time monitoring and data analysis allow for immediate detection and correction of quality issues. Advanced vision systems and sensors can identify defects that might escape human inspection.
## Challenges in Implementation
While the benefits are clear, transitioning to digital manufacturing presents several challenges:
– High initial investment costs for technology infrastructure
– Need for workforce retraining and skills development
– Cybersecurity risks associated with connected systems
– Integration with legacy equipment and processes
– Data management and analysis complexities
## The Future of Digital Manufacturing
As technology continues to advance, digital manufacturing will become even more sophisticated. We can expect to see:
– Greater adoption of autonomous systems and robotics
– More widespread use of augmented reality for maintenance and training
– Development of self-optimizing production systems
– Increased sustainability through better resource utilization
– Deeper integration across supply chains
Companies that embrace digital manufacturing today will be better positioned to compete in tomorrow’s market. The revolution is already underway, and those who fail to adapt risk being left behind in an increasingly digital industrial landscape.