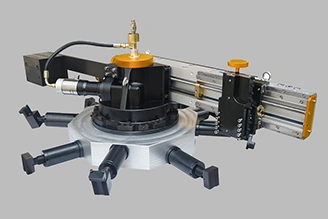
# Flange Facer Machines: Precision Tools for Flange Resurfacing
## What Are Flange Facer Machines?
Flange facer machines are specialized industrial tools designed for resurfacing and machining flange faces to ensure proper sealing in piping systems. These powerful machines play a critical role in maintaining pipeline integrity across various industries including oil and gas, petrochemical, power generation, and shipbuilding.
## Key Features of Modern Flange Facers
Modern flange facing machines incorporate several important features:
– Portable design for on-site machining operations
– Precision cutting tools for accurate surface finishing
– Adjustable cutting parameters for different flange materials
– Stable mounting systems for secure operation
– Variable speed controls for optimal machining performance
## Applications in Industrial Maintenance
Flange facers are essential for:
– Repairing damaged or corroded flange surfaces
– Preparing flange faces for gasket installation
– Creating proper surface finishes for reliable sealing
– Maintaining pipeline systems during shutdowns
– Performing emergency repairs without removing flanges
## Types of Flange Facing Machines
There are several configurations available:
### 1. Portable Flange Facers
These lightweight machines can be easily transported to job sites and mounted directly onto the flange for in-place machining.
### 2. Stationary Flange Facers
Keyword: flange facer machines
Larger, more powerful units designed for shop use where flanges can be brought to the machine.
### 3. CNC Flange Facers
Computer-controlled machines offering the highest precision for critical applications.
## Choosing the Right Flange Facer
When selecting a flange facing machine, consider:
– The size range of flanges you need to machine
– Material types you’ll be working with
– Required surface finish quality
– Portability needs
– Power source availability at job sites
– Budget constraints
## Maintenance Tips for Longevity
To ensure your flange facer machine operates at peak performance:
– Regularly clean and lubricate moving parts
– Inspect cutting tools for wear and replace as needed
– Store the machine in a dry, protected environment
– Follow manufacturer’s maintenance schedule
– Train operators on proper use and care procedures
## The Future of Flange Facing Technology
Advancements in flange facing technology include:
– Improved materials for longer-lasting cutting tools
– Smart sensors for automated depth control
– Wireless connectivity for remote monitoring
– Energy-efficient designs
– Enhanced safety features
Flange facer machines continue to evolve as essential tools for maintaining the integrity of critical piping systems across industries worldwide.