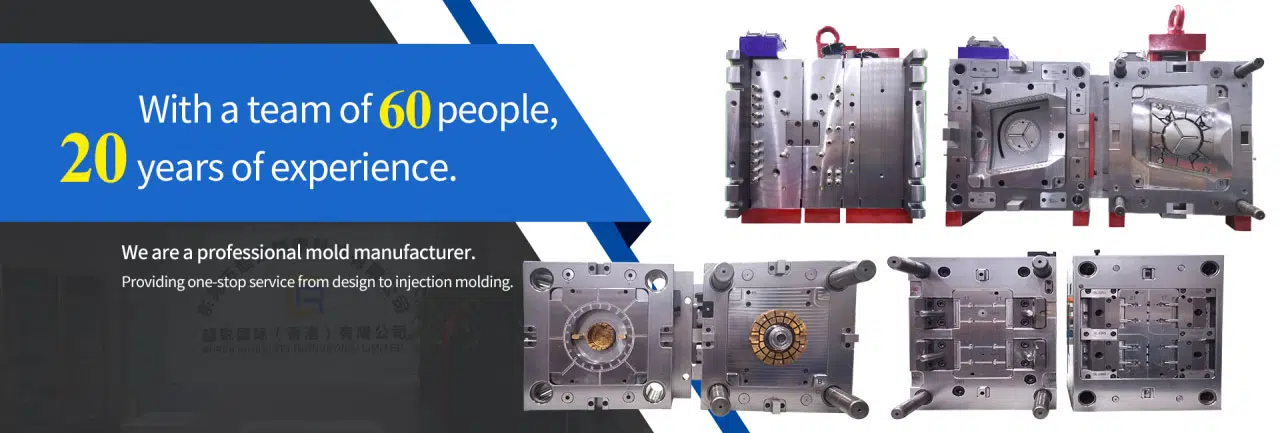
本身
html
Moldflow Simulation in Injection Molding Process Optimization
Injection molding is a widely used manufacturing process for producing plastic parts with high precision and efficiency. One of the key tools for optimizing this process is Moldflow simulation, which enables engineers to predict and analyze the behavior of molten plastic during injection molding.
What is Moldflow Simulation?
Moldflow simulation is a computer-aided engineering (CAE) tool that uses finite element analysis to model the injection molding process. It helps manufacturers visualize how molten plastic will flow into the mold cavity, cool, and solidify. By simulating these processes, engineers can identify potential defects and optimize mold design before physical production begins.
Key Benefits of Moldflow Simulation
1. Reduced Development Time and Costs
By identifying potential issues in the virtual stage, Moldflow simulation significantly reduces the need for costly physical prototypes and trial-and-error iterations. This leads to faster time-to-market and lower development expenses.
2. Improved Part Quality
The simulation helps predict and prevent common injection molding defects such as warpage, sink marks, weld lines, and air traps. Engineers can adjust parameters like gate location, cooling system design, and processing conditions to achieve optimal part quality.
3. Material Optimization
Moldflow allows engineers to test different materials virtually, helping select the most suitable polymer for the application while minimizing material waste during production.
Applications in Process Optimization
Moldflow simulation plays a crucial role in several aspects of injection molding optimization:
- Gate Location Optimization: Determining the optimal gate position to ensure balanced filling and minimize defects
- Cooling System Design: Analyzing and improving cooling channel layouts for uniform part cooling
- Process Parameter Optimization: Determining ideal injection speed, pressure, temperature, and cooling time
- Warpage Prediction: Identifying potential distortion issues and implementing corrective measures
Future Trends in Moldflow Simulation
Keyword: Moldflow Simulation
As technology advances, Moldflow simulation continues to evolve with new capabilities:
- Integration with Industry 4.0 and IoT for real-time process monitoring
- Enhanced predictive analytics using machine learning algorithms
- More accurate material models for advanced polymers and composites
- Cloud-based simulation for improved collaboration and accessibility
By leveraging Moldflow simulation in injection molding process optimization, manufacturers can achieve higher quality products, reduced waste, and improved production efficiency – all while lowering costs and environmental impact.